FABRIC RELAXATION PROCESS: AIR TYPE FABRIC RELAXING IMRPOVE EFFECT
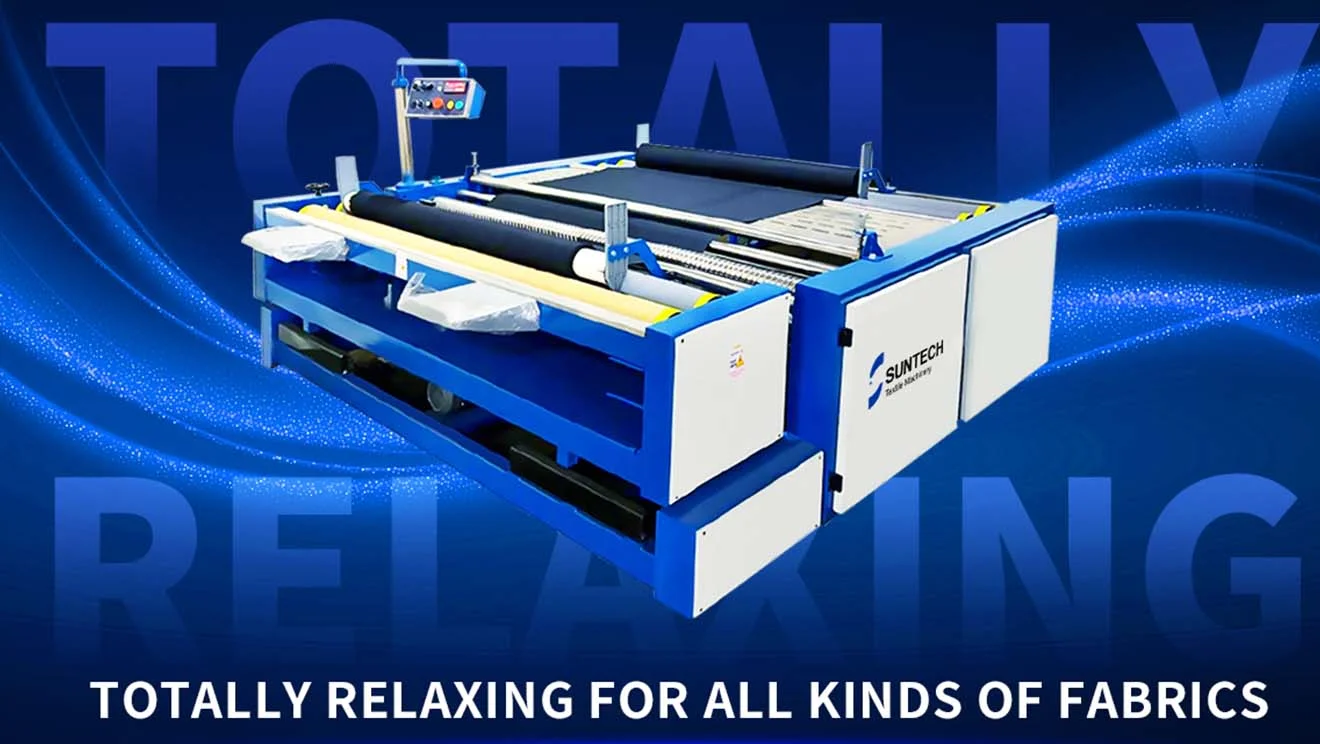
Fabric relaxation involves the process of unwinding fabrics from their rolled state, ensuring they are fully relaxed at ambient temperature before reaching the cutting section. This step holds great significance as it plays a vital role in maintaining the fabric's dimensional stability after the cutting process.
The following are the general way to see about the fabric relaxing method:
Received Fabrics from Warehouse
↓
Fabrics Unrolling through Machine
↓
Keeping Fabrics in Relaxation Rack in a certain period
(Relaxation time will depend on Fabrics Nature)
↓
Fabrics spread/ Lay for cutting
↓
Relax Fabrics
↓
Start Cutting
Fabric relaxation is an indispensable process that demands careful attention. The entire outcome of fabric cutting, shaping, and measuring depends heavily on the correct treatment during this stage. The primary purpose of fabric relaxation is to ensure that the fabric retains its intended shape and dimensions even after being cut.
Traditionally, fabric relaxation took anywhere between 12 to 48 hours, and an additional two hours after laying. The specific duration depended on various factors, such as the fabric's inherent nature and the preferences of the buyer or manufacturer regarding fabric relaxation. However, waiting for such extended periods could be deemed inefficient, leading modern mills to seek alternative solutions.
In response to this challenge, fabric mills have embraced the assistance of fabric relaxing machines, significantly reducing the time needed for fabric relaxation while maintaining quality and accuracy. These machines have proven to be game-changers in the industry by streamlining the fabric preparation process.
Several types of fabric relaxing machines are available, each offering its unique features and capabilities to cater to different fabric types and production requirements. Here are some of the most common types:
1. Steaming Machines: These fabric relaxing machines utilize steam to relax the fabric fibers, making them more pliable and easier to work with. The steam softens the fibers, reducing tension and stress within the fabric, ultimately enhancing its stability.
Mechanical Relaxing Machines: Mechanical relaxing machines employ a gentle mechanical process to relax the fabric. By applying controlled tension and release, these machines help to ease any stiffness or strain present in the fabric, ensuring better handling during subsequent stages.
2. Air Type Relaxing Machines: Air type relaxing machines utilize the power of air to create a cushioning effect, which aids in relaxing the fabric. The controlled flow of air allows the fabric to loosen up and reduce any creases or wrinkles, resulting in improved fabric quality.
Choosing the appropriate fabric relaxing machine depends on the specific characteristics of the fabric and the desired outcome. Manufacturers and buyers must consider factors such as fabric type, weight, and intended usage to ensure optimal results.
Fabric relaxation remains a crucial step in the production process, as it directly impacts the final quality of the fabric after cutting. The adoption of fabric relaxing machines has revolutionized this process, making it more efficient and time-saving for modern mills. By employing the right fabric relaxing machine, manufacturers can maintain the integrity of their fabrics and enhance overall production efficiency.
SUNTECH Fabric Relaxing Machine (ST-FRM-VI) has earned the distinguished title of being the Global Sales No.1. Its primary purpose is to eliminate tension from knit fabrics, ensuring they remain neat and organized during storage. Unlike the traditional method of transitioning from rolled to plaited fabric relaxation, this advanced machine offers the perfect solution by unwinding and relaxing the roll with consistent tension, resulting in flawlessly prepared fabric rolls.
In essence, the fabric relaxing machine streamlines the process, enabling direct movement to the cutting section, eliminating the need for a 24-hour laying time. This remarkable feature significantly enhances efficiency, saving valuable time before the cutting stage.
The machine's capabilities extend further with the integration of a special air floating device and a tension control system. These innovative additions ensure that fabric tension is entirely released from one roll to another, thereby minimizing the occurrence of out-of-tolerance cut parts. This contributes to a more precise and high-quality cutting process, ultimately improving overall production efficiency.
SUNTECH Fabric Relaxing Machine (ST-FRM-VI) stands out as the leading choice globally, offering an efficient and effective solution for eliminating fabric tension in knit fabrics. Its ability to directly transition to the cutting section saves substantial laying time, making it a time-saving and productivity-enhancing asset for manufacturers. Furthermore, the machine's state-of-the-art features, including the air floating device and tension control system, guarantee a reduction in out-of-tolerance cut parts, ensuring a flawless end product.
Comments
Post a Comment