SUNTECH MOTORIZED WARP BEAM TROLLEY
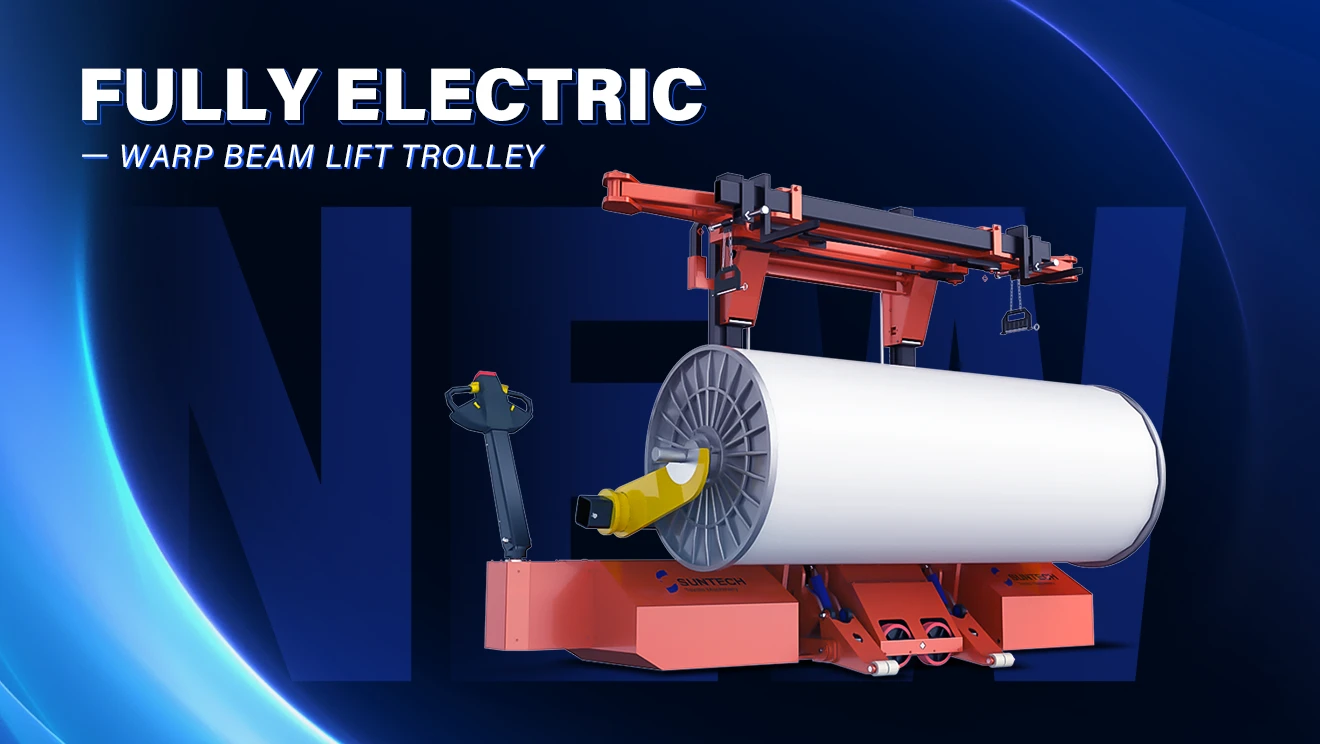
Over the past four years, the COVID-19 epidemic has significantly impacted various sectors, including the warehousing and logistics industry. This industry, known for its fast-paced nature, has faced unprecedented challenges. As a result, there has been a substantial increase in the demand for transformation vehicles and material handling equipment. To address this need, the SUNTECH motorized warp beam trolley with AGV technology emerges as the ideal solution for the textile industry. It enables intelligent and automated material handling processes.
Operating a warehousing and logistics system incurs several fixed costs, namely site rental costs, labor costs, and transportation costs. Unfortunately, these costs have been steadily rising, particularly labor costs, which have been further exacerbated by the arrival of the COVID-19 epidemic. This has inflicted significant damage on the warehousing and logistics industry.
Reducing labor costs and enhancing intelligent operations to automate and streamline manual handling processes has emerged as a critical challenge for professionals in the warehousing and logistics industry.
Introducing the ST-MBT-02I from SUNTECH Textile Machinery, a cutting-edge motorized warp beam trolley designed specifically for efficient bottom beam transportation. This latest model is capable of seamlessly inserting into weaving machines and transporting weaving beams weighing up to 1800kg, with customizable beam widths. Additionally, it offers an additional loading capacity of 300kg for the harness, further enhancing its versatility and functionality.
The ST-MBT-02I SUNTECH motorized warp beam trolley is a versatile solution that can be seamlessly integrated with weaving machines of various working widths, ranging from 170cm to 340cm, without requiring any modifications.
The trolley effectively accommodates the harness through its standard take-up for harness frame, contact rails, dividing rails, or the complete warp stop motion system.
Despite the potential advantages of Automated Guided Vehicles (AGVs), many companies in the warehousing and logistics industry still rely on traditional manual labor practices. This is primarily due to the early stages of digital and intelligent transformation within these enterprises, as well as insufficient industry education regarding the benefits of AGVs.
In recent years, the domestic market has seen labor costs remain significantly lower than the expenses associated with technological reforms. AGVs, without clear efficiency advantages, have not gained widespread adoption as a solution to address logistics challenges.
However, the warehousing and logistics industry has long struggled with labor shortages or difficulties, which have been further exacerbated by the impact of the ongoing epidemic. Consequently, the epidemic presents an opportunity for the AGV industry to flourish. The potential benefits outweigh the challenges, making it conducive to the widespread adoption and promotion of AGVs within the industry.
When compared to manual labor and traditional forklift equipment, AGV (Automated Guided Vehicle) equipment offers a distinct advantage in terms of flexibility.
AGV Beam Transport Trolleys come in various types, categorized by different factors:
Navigation Methods:
- Direct coordinate navigation method
- Electromagnetic navigation method
- Magnetic navigation method
- Laser navigation method
- Optical navigation method
- Inertial navigation method
- Image recognition navigation method
- GPS (Global Positioning System) navigation method
Drive Modes:
- Single drive
- Differential drive
- Dual drive
- Multi-wheel drive
Transfer Methods:
- Push-pull type
- Roller type
- Chain type
- Belt type
- Traction type
- Piggyback type
- Fork type
- Picking type
- Gantry type
- Robot type
Communication Methods:
- Wired communication
- Infrared light communication
- Radio communication
- Wireless local area network
These variations in AGV equipment provide a wide range of options to suit specific needs and enable efficient and effective material transportation and handling operations.
By implementing an intelligent system, AGV axle vehicles can operate independently along predefined routes, eliminating the need for manual intervention and enabling round-the-clock operation. This not only enhances operational efficiency but also significantly improves stability. For modern enterprises, embracing this change has become imperative.
AGV automated warehousing and handling equipment seamlessly integrates with MES (Manufacturing Execution Systems), ERP (Enterprise Resource Planning), WCS (Warehouse Control Systems), and other systems. This integration allows for fully flexible and highly automated modern logistics, enabling enterprises to achieve modularization, intelligence, and simplicity in their management approach. Consequently, it elevates factory automation to new heights.
SUNTECH Textile Machinery, a professional global enterprise with decades of experience and research, is dedicated to providing customers with innovative products such as motorized beam trolleys that incorporate AGV technology. In addition, SUNTECH Textile Machinery offers excellent services, with a team of experienced experts available for timely and effective support throughout the entire customer journey. From pre-sales consultation to sales, maintenance, and comprehensive after-sales assistance, SUNTECH Textile Machinery strives to deliver the ultimate and comprehensive service experience to its valued customers.
Comments
Post a Comment